Original wear parts are made of black or HB steel and sometimes have to be replaced at very short intervals, which leads to high maintenance and operating costs for the machine.
In collaboration with EVM Margarethen am Moos and BioG GmbH, DURAPARTS has developed an innovative solution and brought it to market maturity: Hardfaced linings and impact tools that significantly increase wear resistance.
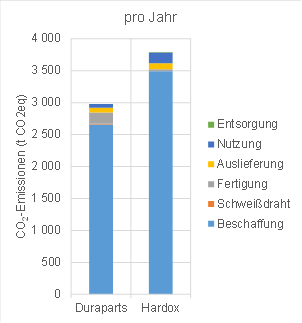
These HVF components have a service life that is up to four times longer and only cost a maximum of twice as much as conventional parts. The resulting operating cost savings for the system operator can reach a remarkable 60% per year.
In order to also investigate the ecological footprint of this technology, we worked with the team of Prof. Posch and Dr. Feichtinger from the Industrial Engineering Department (WBW) at the Montan University in Leoben and with the support of the Austrian Research Promotion Agency (FFG) carried out a comprehensive analysis. The life cycle analysis (LCA) results show that DURAPARTS HVF cladding also enables CO2 savings of up to 25% per year.
These findings are based on a thorough analysis of energy consumption along the entire value chain, from raw materials to disposal. The linings made from DURAPARTS HVF sheets and Hardox® original components were compared here. The Umberto tool used under license by the WBW proved to be extremely helpful.

However, the static comparison of the current state was only the first step in the WBW’s work. Things got really exciting when various scenarios were developed as to how the 25% savings potential mentioned above could be increased even further. Our developers are now working intensively on optimizing the individual input factors, especially the transport chains for raw material purchases and the quite energy-intensive process of deposition welding of our HVF metal sheets, which are used as raw material for the linings.
Thanks to the calculation tool developed by WBW, we are now able to compare and optimize other alloys and substrates; for biogas shredders but also for shredders in the areas of recycling, gravel & crushed stone as well as raw material processing for the paper industry.
I am enthusiastic about the study results and see the output as clear evidence that DURAPARTS is investing in the right technologies and is indirectly making a strong contribution to reducing CO2 emissions.
BioG GmbH, technology leader in biogas feeding technology, is our global sales partner for these innovative components. Together we have been optimizing the performance of shredders and conveyor systems in the biogas market for years.
EVM – Energieerzeugung Margarethen am Moss GmbH operates the largest and most integrated biogas plant in Austria and uses shredders from several manufacturers, which gives us the ideal test environment for new materials.